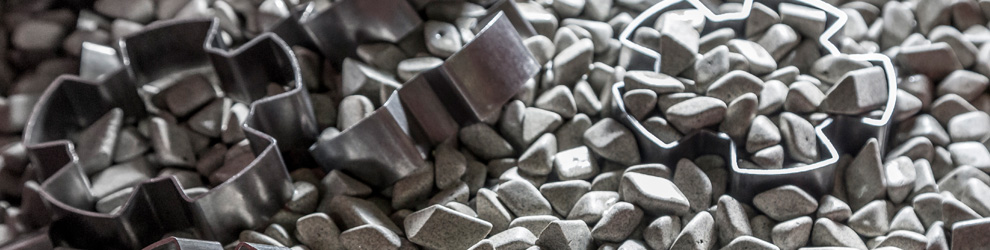
Deburring
No sharp edges left
When workpieces are machined, e.g. by grinding, sharp edges, burrs or very fine chips are created. These may become an incalculable risk with regard to the proper function of the final product and they might even pose the risk of physical injury. However, these risks can be prevented by contracting PAUL JORES GmbH’s professional deburring service. We give your workpieces the perfect surface finish and your parts can be used without further ado.
Vibratory grinding and brush deburring with post-treatment: washing, drying & preserving included
Our modern machines efficiently deburr the workpieces either in batches or in a continuous process. Two kinds of ground workpiece deburring services are available: vibratory grinding in a rotary vibrator or brush deburring with a planetary brush head. For the vibratory grinding process, the workpieces and abrasive media are placed into the rotary vibrator. The vibratory action causes the media to rub against the workpieces and by this achieves the desired result. Brush deburring is ideally suited for flat surfaces. In a continuous process, special brushes remove burrs and if required the surface can be super-finished up to mirror finish. After the finishing process, the pieces are washed, preserved and dried in our washing equipment. Upon request, your workpieces can be provided with a defined maximum surface tension, they can undergo a visual inspection and each part can be packed individually.
Learn more about our other grinding services!